What To Know
- The HIMA FlexiSILon solution creates a much safer turbomachinery plant with much lower operating costs and higher financial returns, especially critical in today’s oil and gas plants.
- “We look forward to continue to nurture and grow with all our valued Malaysian and Asian oil and gas customers to ensure superior industrial and automated safety, in the spirit of protecting people, businesses, and the environment,” said Best.
Editor’s brief: Leading automated safety solutions vendor HIMA advises Malaysia industries to adopt smart safety industrial solutions for better safety, cybersecurity, and profitability. Read more below.
SINGAPORE – Malaysian business leaders are urged by HIMA, a global leader in automated safety systems, to use cyber-safety and profitability-enhancing smart safety industrial solutions in the modern, digitally-enabled manufacturing environment.
HIMA has worked with major corporations including Malaysia LNG and BASF-Petronas Chemical to offer smart safety solutions, such as functional safety for emergency shutdowns, fire, and gas systems.
The annual cost of an unexpected outage can easily reach seven figures. Just 3.65 days of unscheduled downtime annually can cost businesses US$5.037 million, according to a study by Kimberlite. Unplanned downtime costs the offshore oil and gas industry an average of US$38 million per year, or 27 days. This amount can go as high as $88,000,000 in very extreme circumstances.
“In the era of Industry 4.0, everything is interconnected. The more complex industrial plants become, the more rigorous the requirements that are imposed on functional safety. Therefore, safety systems must be just as smart as the production processes of the future,” said Friedhelm Best, Vice President, Asia Pacific, HIMA. “Digitization creates entirely new requirements for plant operators in the industrial sectors. They need solutions that not only protect plants and employees in the event of a disaster, but also effectively counter cyber-attacks and boost the long-term profitability of plants.”
He added that HIMA’s smart safety solutions for industrial applications are currently used in various industries particularly in oil and gas, chemicals, energy and rail.
HIMA’s latest Industrial safety technology is being showcased at the 20th Asian Oil & Gas Conference (AOGC), from 23 to 25 June 2019, at Kuala Lumpur Convention Centre in Malaysia. The conference is graced by HE Tun Dr Mahathir Mohamad, Prime Minister of Malaysia and hosted by Petronas.
Around the world, the functional safety of turbines and compressors is becoming a focal point of industry. A small accident can have catastrophic consequences, endanger human lives, and incur high costs from losses and lawsuits.
A turbomachinery (TMC) such as turbines are often found in oil and gas plants, as well as many other critical infrastructures. They are typically controlled by many disparate components by diverse manufacturers integrated into a complex structure. As such, turbomachineries can often incur expensive engineering costs, take up massive spaces, house complex wiring, use different and sometimes non-interoperable communication standards, resulting in fragile implementations that are prone to faults and challenges in troubleshooting. The International Electrotechnical Commission has introduced stricter safety standards, which can now be met with a single system for safety and critical control. FlexSILon TMC ensures all turbomachinery runs safely.
The HIMA FlexSILon TMC with HiMax is an integrated solution that provides safe and cost-effective turbomachinery operation. The system combines all individual components and include overspeed protection, into a singular system that possesses high functional safety and flexibility. The system provides simulation and machine monitoring of all turbomachinery, and manage functions such as turbine operation and control, turbine protection (such as overspeed prevention and mitigation), compressor operation and control, compressor protection, emergency shutdown (ESD), and human-machine interface (HMI). As a result, the HIMA FlexiSILon solution creates a much safer turbomachinery plant with much lower operating costs and higher financial returns, especially critical in today’s oil and gas plants.
FlexSILon TMC monitors, regulates and controls turbomachinery centrally, enabling companies to save more than US$500,000 per year, compared to using individual systems, while reducing failure rate and overall operating expenses, and gaining higher productivity.
“We look forward to continue to nurture and grow with all our valued Malaysian and Asian oil and gas customers to ensure superior industrial and automated safety, in the spirit of protecting people, businesses, and the environment,” said Best.
Automated Safety for key installations in Malaysia
In the early 1990s, HIMA established a presence in Malaysia; now, HIMA Malaysia is a wholly owned subsidiary of the HIMA group, backed by a worldwide organization of TÜV-certified engineers and specialists.
Even the most demanding industries, like the oil and gas sector, can be appeased by HIMA’s intelligent safety solutions, which meet all SIL 3 and SIL 4 regulations. Since HIMA has a local office in Malaysia, it can better anticipate and address the unique safety concerns of its Malaysian clientele.
For more information on HIMA’s turbomachinery solutions, visit https://www.hima.com/en/industries-solutions/turbomachinery-tmc.
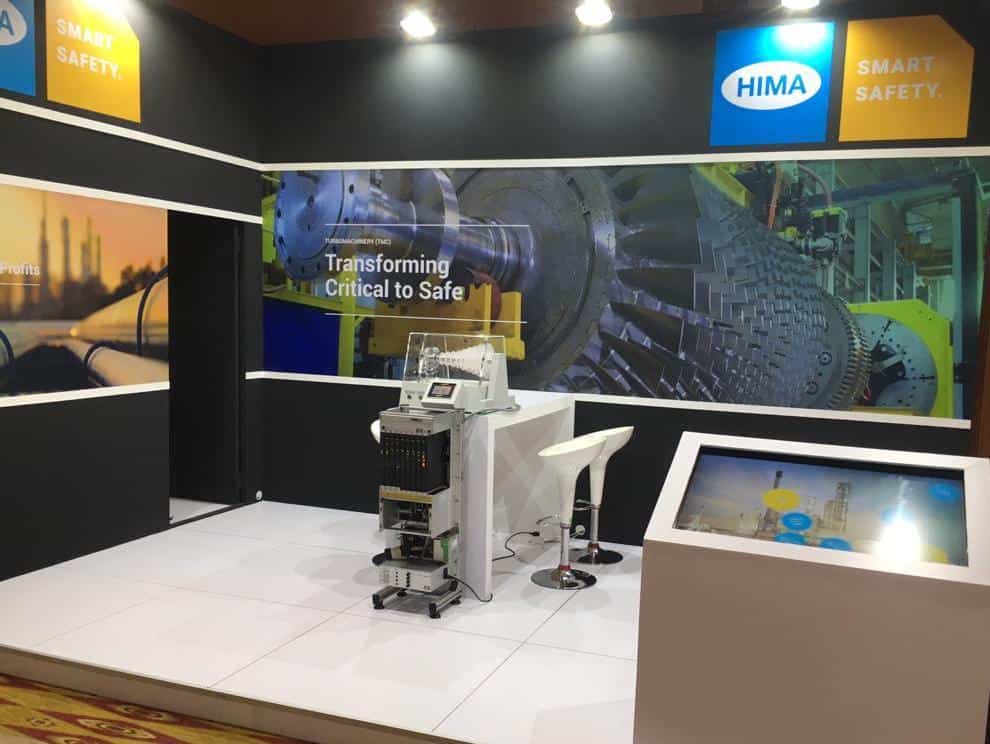
###